What are the Benefits of Selecting Zinc-Coated Metal for Commercial Building Products?
Many manufacturers of non-structural commercial building products offer some type of zinc-coated steel, but how do you know which one is best for your application?
Steel products with a zinc finish are available in several forms, including galvanized, galvannealed, electro-galvanized, zinc-coated and hot-dipped, all of which provide corrosion-resistance against rusting of carbon-based steel.
How do zinc-coated metals prevent and control rust?
A zinc coating is either applied to steel in sheet form in the steel mill, or to a finished product made of steel. The coating acts as a barrier that isolates and protects the base metal from the environment. After steel has been treated with a zinc coating, any exposure to atmospheric oxygen creates a zinc oxide layer, exposure to water creates zinc hydroxide, and zinc carbonate film forms when exposed to carbon dioxide, protecting the underlying steel from exposure to rust-causing moisture. Even if the steel or paint is scratched, damaged or the edges cut, zinc carbonate fills in the area to protect the steel beneath the zinc coating on both painted or unpainted products.
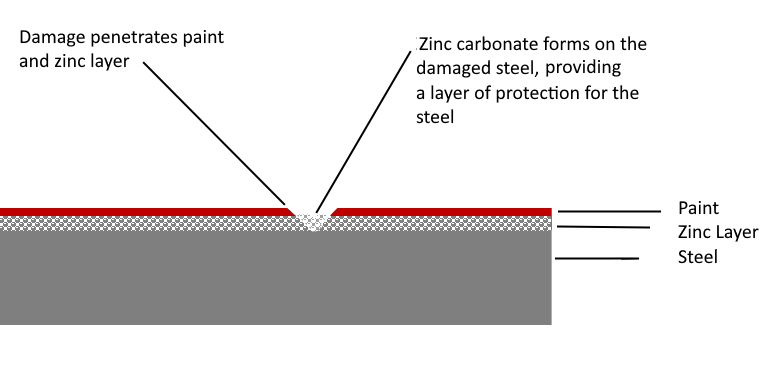
What are Architects, Specifiers, Contractors and Building Owners Looking for when they Specify a Zinc-coated Building Product?
- Meets product specifications for that product type including ASTM standards for zinc coating thickness or weight
- Will stand up to conditions such as exterior use, corrosive or humid environments
- A product that meets building code
Common Types of Zinc-Coatings on Steel
GALVANNEAL SHEET STEEL
Galvanneal sheet steel is produced by passing sheet steel in coil form through molten zinc in the steel mill at high speed. A gas wiping process is used to control the thickness, then the steel is heated in an annealing furnace at temperatures up to 1050°F causing the iron in the steel to bond permanently with the zinc coating. The coating penetrates the metal, strengthening the material to form an iron-zinc alloy underneath the zinc. EQ coatings are an additional treatment that are applied to non-structural studs zinc-coated sheets that fill cracks and voids in the zinc layer.
Coating Standards: Coating weight minimums are established by ASTM standard 653A measured in oz/ft² using a designation such as A40 which has a coating weight of .20 oz/ft² per side of the sheet. Common coating weights are A25, A40, A60.
Appearance & Paintability: Galvannealed is a dull gray in color and has a matte surface that does not require a primer for paint. The paint can mechanically “lock” with the zinc-iron crystals on the surface, forming an excellent paint bond.
GALVANIZED SHEET STEEL
Galvanized sheet steel also known as hot-dip galvanized, is manufactured in a steel mill using a similar process to galvanneal steel including gas knives to control coating thickness, but does not include a final heat treatment. The result is a layer of zinc iron alloys deposited on the surface of the steel.
Coating Standards: Coating weight minimums are established by ASTM standard 653A and measured in oz/ft² using a designation such as G40 which has a coating weight of .20 oz/ft² per side of the sheet. Common coating weights are G30, G40, G60, G90.
Appearance & Paintability: Galvanized steel has a mottled light and dark surface and is so smooth that it can be difficult to get paint to adhere to untreated metal. Galvanized steel must first be cleaned with alkaline or acid and then “profiled” to provide a textured surface for primer and paint to adhere to.
ELECTROGALVANIZED SHEET STEEL
Zinc coatings are applied to steel sheet by electrodeposition in a continuous process at the steel mill. The coating of pure zinc is thinner than continuous sheet galvanizing and is mechanically-bonded to the steel, but provides a smoother finish with no alloy layers.
Coating Standards: Coating weight minimums are established by ASTM standard A879/A879M and measured in in oz/ft² or the SI system in g/m², using a designation such as 13Z13Z which has a coating weight of .13 in oz/ft² per side of the sheet. Common coating weights in oz/ft² are 08Z, 13Z and 30Z .
Appearance & Paintability: Electrogalvanized steel has a smooth finish that may be dull or shiny and most do not require a primer for paint, resulting in an excellent paint bond to the absorbent zinc surface.
ZINC-PLATED PARTS
Products that are fabricated of cold-rolled steel can have a zinc coating applied to the finished item. A layer of zinc is applied by immersing the steel object in an ambient temperature zinc sulphate solution using an electrolytic deposition process. The zinc coating consists of pure zinc that tightly adheres to the steel. One benefit of coating finished objects, is that all surfaces – inside and out receive a coating of zinc providing an unbroken protective layer. An electrogalvanized or zinc-plated coating produces a thinner and therefore, less corrosion-resistant coating than galvannealed or galvanized coatings.
Coating Standards: Coating thickness minimums are established by ASTM standard 633 using a designation such as Fe/Zn 25 which has a coating thickness of 25 µm or 0.984 mils on the entire part. Coating classifications range from Fe/Zn 5 for indoor use to FE/Zn 25 for exposure to harsh conditions.
Appearance & Paintability: Depending on the additives used in the process, zinc-plated products may have a smooth, shiny or matte surface that does not require a primer for paint resulting in an excellent paint bond to the absorbent zinc surface.
HOT DIP GALVANIZED PARTS
Hot-dip galvanizing is a process used to add a zinc coating to finished steel articles. The items are immersed in a molten zinc bath, during which the zinc reacts with iron in the steel to form a series of zinc-iron inter-metallic alloy layers.
Coating Standards: Coating thickness minimums are established by ASTM standard A123, A153 and A767. A123 is for structural steel made from rolled, pressed and forged shapes, castings, plates, bars, strips and fabricated products. A153 is for hardware products such as castings, fasteners, rolled, pressed and forged products. A767 is for steel bars for concrete reinforcement. Those standards require a minimum average coating thickness by either Class 1 (350 oz/ft²) or Class 2 (2.00 oz/ft²).
Appearance & Paintability: Appearance can vary and be matte, gray, shiny or spangled. The surface is so smooth that that it can be difficult to get paint to adhere to untreated metal. Products with a hot dip finish must first be cleaned with alkaline or acid and then “profiled” to provide a textured surface for the primer and paint to adhere to. Many hot dip galvanized parts such as nuts and bolts, are not intended to be painted.
COMPARING THICKNESS OF ZINC COATINGS
Corrosion performance is approximately linear, based on the thickness or coating weight and type of environment to which it is exposed. The thicker the coating, the longer the steel underneath is protected, and painting the product extends the life even more. The chart below shows the ASTM standards for each type of zinc coating with examples.
Galvanized, Galvanneal and Electrogalvanized sheet steel is measured by the deposition on the surface area in oz/ft² or gm/m². For instance, a coating weight of A60 or G60 would have .30 oz/ft² per side of the sheet, and would have roughly twice the amount of zinc as a coating weight of A30 or G30.
Zinc-Plated and Hot Dipped products that are immersed in the zinc coating are measured in microns of coating thickness, which is not directly comparable to the “coating weight” of galvanized and galvanneal sheet steel.
ASTM Standards for Each Type of Zinc Coating:
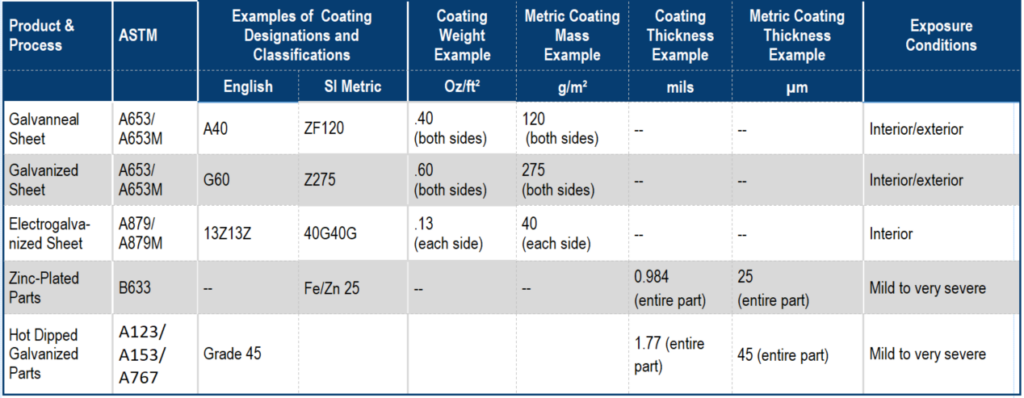
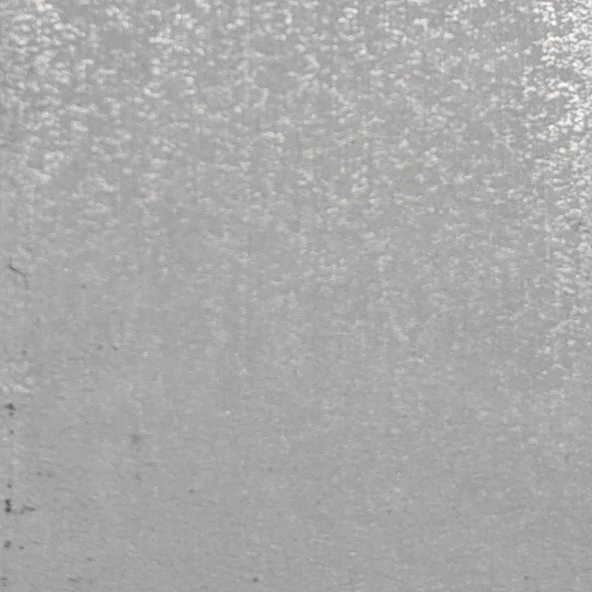
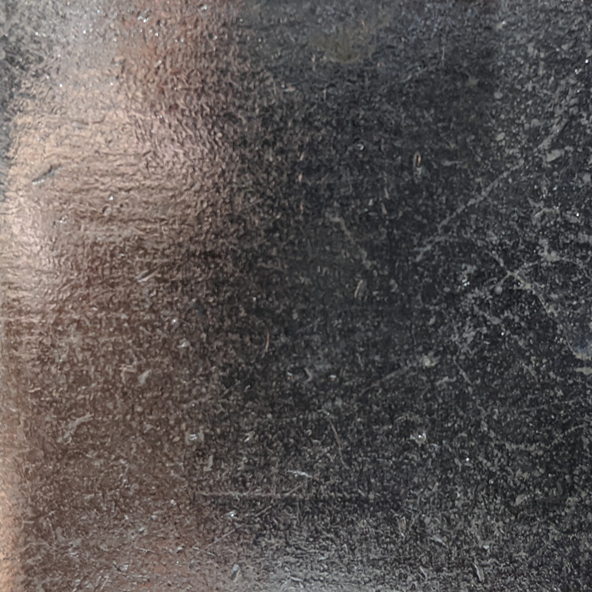
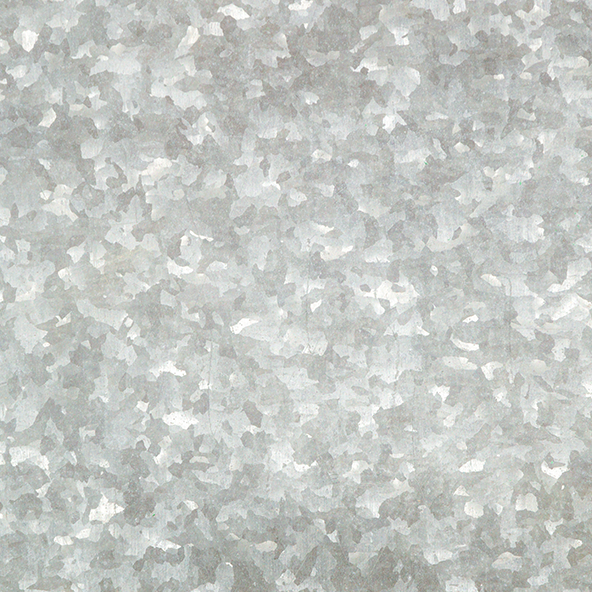
COMPARISON OF MATERIALS – GALVANNEAL, GALVANIZED, STAINLESS STEEL AND ALUMINUM
Characteristic | Galvanneal Steel | Galvanized Steel | Stainless Steel | Anodized Aluminum |
Coating | Three zinc-iron layers Harder and more durable | One zinc layer | Solid material throughout | Protective oxide layer |
Appearance | Dull gray matte appearance | Shiny metallic appearance | Various finishes from mirror-like to brushed | Slightly dull metallic, multiple color options |
Paintability | Higher paintability, better paint adhesion with minimal pre-treatment | High paintability with profiling and priming pre-treatment of metal | Usually not painted, but has higher paintability and paint adhesion. Primer not needed | Usually not painted, but has moderate paintability |
Formability & Welding | Higher formability and excellent weldability | High formability, mod-erate weldability. Zinc coating can burn away. | Higher formability and excellent weldability | Higher formability, good welding |
Corrosion Performance | Higher corrosion-resistance when combined with powder-coat paint finish | Higher corrosion-resistance, can be used for exterior appli-cations. Not always painted. Not recom-mended for exposure to chlorinated water. | Highest corrosion-resistance. Not recom-mended for exposure to chlorinated water. | Higher corrosion-resistance. Aluminum is the most corrosion-resistant material for exposure to chlorinated water |
Cost | Higher cost, but better value | High cost | Highest cost | Lower cost |
Is there a Benefit to Painting Zinc-coated Products?
When the two corrosion protection systems; painting; and zinc-coated steel are used together, the result is termed a “Duplex System”. The paint layer protects the underlying zinc coating and the zinc coating protects the steel, providing longer product life. If the paint layer is damaged, the zinc coating will begin to corrode, forming zinc carbonate at that site—creating a barrier between the environment and the steel and preventing rust.
· Due to the iron content of galvanneal steel, it is recommended that those products be painted for the best durability.
· Products that are factory painted, undergo cleaning, pre-treatment and drying as part of a process to achieve good paint adhesion.
· If a product is factory primed, it is important to finish the product in the field with a quality paint, as primers are not intended to provide the same protective characteristics as finish paint.
· Products made of galvanized sheet steel that have been formed or welded may have spots where the zinc coating has flaked or burned away, leaving bare spots that are unprotected, so paint will be the only barrier coating in those areas.

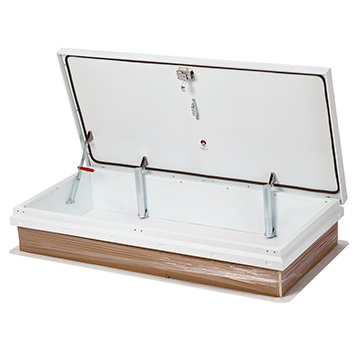
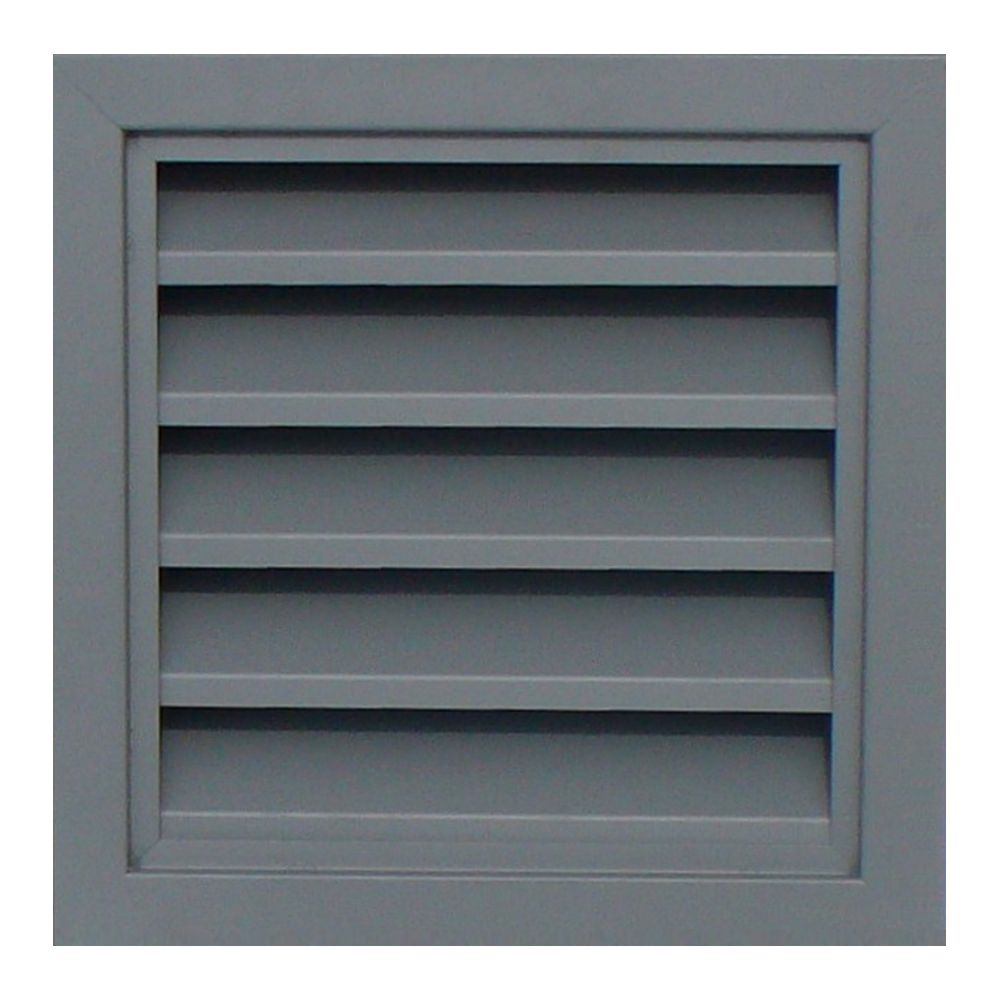
Options for Painting Zinc-coated Products
Powder coating is a toxin-free, environmentally-friendly process that applies a polymer-based powder to metal and is then cured with heat. Powder coat paint is durable, available in a range of colors and can provide a protective coating that will last for years. This process is extremely efficient reducing waste by 95% over wet-applied paints and provides a thicker, more durable coating. Many manufacturers state that powder coated products can be repainted in the field.
Wet-applied paint or primer is usually applied as paint in a solvent-based solution. This paint is typically for small quantities of products. The wet-applied process can use toxic solvents and volatile organic compounds that are harmful if inhaled and is less environmentally-friendly than powder coat. Many manufacturers state that powder coated products can be repainted in the field.
Other paints that are compatible with hot-dip galvanized steel, such as epoxy-polyamide, acrylics, vinyls, and latex-acrylics may be used with proper surface preparation. Consult the building product manufacturer for recommendations.
Environmental Considerations
Galvanized steel can be made from recycled steel and typically uses about 30% recycled zinc. It can be recycled in a similar way to other steel products. During the process, the zinc material is collected and recycled.
Resources to Learn More:
American Galvanizers Association https://galvanizeit.org/
The Galvinfo Center (International Zinc Association) www.galvinfo.com
Finishing.com www.finishing.com
Visit our Website
Product submittals indicate material options. Most steel roof accessories are fabricated from galvanneal steel.
Note: This document is intended to provide general information only. For specific information, contact your building material supplier about their products.